![]() | ![]() |
Lean: focus on what adds value and eliminate what does not
Keycare uses Lean to develop practical action plans to suit the requirements of your organization.
Keycare uses tools like TAKT time, KanBan, Kaizen, Gemba, Poka Yoke, Jidoka, for Lean implementation - these are put in place to facilitate improvements to your business.
Lean concepts have reached many industries - the variety of organizations that are practicing lean concepts demonstrate the universal applicability of Lean concepts and Lean thinking. Although Lean thinking is universal, Lean technologies are unique to each implementation.
It is important to understand that Lean is not about just tweaking the current systems. It is a conceptual change to the system. This requires lots of change management and care for people. People are the most important resource. Lean is not about cutting head count or corners. It is about the elimination of waste from the system…continuously. Many implementations of Lean fail due to the lack of understanding on basic Lean concepts and general knowledge, not because of the problems in Lean itself.
We have assisted Lean companies bring in their customers and suppliers to the Lean process. Keycare helps each other in the process of value creation and ultimately getting rewarded collectively for each of their efforts. Large amounts of waste normally exist within the interfaces where each party is separated in the supply chain. In today's competitive markets, you need to treat your suppliers and customers as partners, and not as separate parties.
Effective implementation of Lean results in lower cost, higher quality, ability to supply on demand, waste-free operations, eco friendliness, and human resource development. Among the key features of Keycare's approach to Lean:
- Empowerment to and respect for people; idea generation and using of ideas generated by employees for the betterment of the organization
- Organic management structures
- Ability to adopt to fast changing situations
- Simplicity
Keycare's approach for Lean is straightforward...with its goal to only focus on what adds value and eliminate what does not. Keycare works on overall fulfilment system to achieve more value for your company by properly designing internal processes and downstream processes…we have found that it is best to start with the customer and work backwards.
The goals for Lean cannot be achieved using traditional methods. Keycare's straightforward approach results in adding value to:
- Shrinking supply chain
- Lower Inventory
- Reduce Lead Time
- Fill Product to Customer when they need it
General Outline for Keycare Lean
Document and Map Process Flow
- List processes and sub processes
- List equipment and machines
- Incorporate material handling and storage space requirements
- Incorporate labour requirements
- Document process with work flow chart
Action Plan
- Catalogue all activities
- Develop Solutions Matrix
- Counter measures for root cause
- Practical solution for each root cause (can have several practical solutions)
- Assess Effectiveness x Feasibility x Cost Benefit
- Identify resources needed for each action plan step and potential barriers
- Mitigate potential barriers
- Set due date
Kaizen
- Work with department groups on focused/quick event/area – specific improvements
- Streamline workflow….handling, movement, reduce batch sizes, eliminate bottlenecks and points of congestion, minimize wait times
Gemba
- Go to the site/place where value is created
- Problems are visible and improvement ideas come from here (eg. reduce change over and set up times)
Remove Waste
- Waiting (people & equipment)
- Inventory (raw material, WIP)
- Transportation (movement of product/service)
- Overproduction
- Over Processing (more value than customer wants)
- Motion
- Intelligence
- Rejects/Scraps
Poka Yoke
- Mistake proofing for product defects and human errors
- Improve material management & flow
Kanban
- Pull from actual demand from customer
- What to produce
- When to produce it
- How much to produce
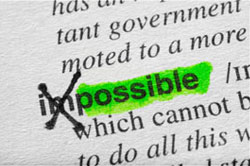
Keycare Helped Us Zero-in on the Priorities
"The Royal Alexandra Hospital Foundation needed to take a fresh look at our strategic planning process and strategic plan. Tom Keogh and Keycare laid out a very clear yet detailed process that worked, and ensured that our organization’s leaders, members, and stakeholders were engaged. Keogh/Keycare effectively guided us through the process, helped us zero-in on the priorities, and develop a strategic plan that is well-suited and practical - best of all, they got our management team involved in developing and delivering the Action Plans from the Goals and Objectives. Their flexibility, creativity, team approach and focus made all the difference - they exceeded our expectations."
Andrew Otway, President & CEO,
Royal Alexandra Hospital Foundation